„All-In-One“-Dichtungen dichten nicht nur, sie können auch befestigen, abstreifen und führen. Dabei sind sie – falls nötig – gleichzeitig Teil des Gesamtbauteils.
Konstruktive Erfordernisse, insbesondere die Notwendigkeit, Raum und Gewicht einzusparen, führen zwangsläufig zu dem Wunsch, Bauteilfunktionen zu erhöhen bzw. zu verdichten. Beispielsweise ist oft kein Platz vorhanden, um eine Nut mit beidseitigen Wandungen für einen O-Ring unterzubringen. Oder Aufnahmenuten für Nutringe oder Abstreifer können nicht tief genug eingestochen werden. Bei einer All-In-One-Dichtungsbuchse von SKF Economos werden Dichtlippen für die dynamische Abdichtung, statische Dichtkanten und Abstreifer direkt am Träger angebracht. Zur Buchse gehört eine Bohrung mit Verteilerrille, durch die Schmierstoff zugeführt werden kann.
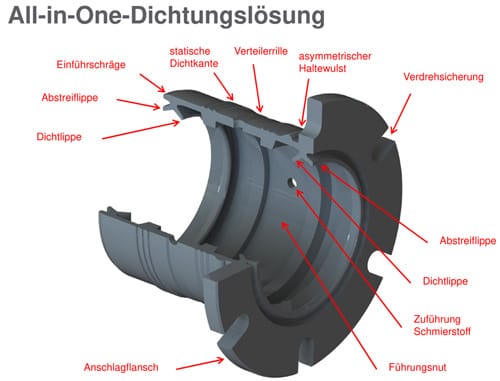
Click to Zoom.
Das kompakte Bauteil lässt sich erheblich leichter und schneller einbauen als einzelne Komponenten, da keine Dichtungen von innen montiert und kalibriert werden müssen. Weitere Features erleichtern die Montage zusätzlich – gleichgültig, ob diese durch Fertigungsautomaten bzw. Roboter oder manuell erfolgen soll: Hierzu gehören eine Einführfase, die das Montieren der Buchse vereinfacht, sowie eine Verdrehsicherung, Aussparungen am Flanschumfang sowie der Anschlagflansch selbst zur sicheren Positionierung.
Montageaufwand reduziert sich
Der asymmetrische Haltewulst hat in Montagerichtung einen flachen Winkel und auf der Gegenseite (Halteseite) einen steilen Winkel, um die Fixierung zu sichern. Zuführeinheiten und Kalibrierprozesse für die Einzelkomponenten werden damit überflüssig. Durch den Wegfall von Montagekomponenten für das Aufziehen der Einzeldichtungen auf den Träger reduzieren sich die Montagekosten. Gegenüber einzeln aufzuziehenden O-Ringen für die statische Dichtung mit Abmessungen von 6 mm x 0,5 mm verfügen die kompakten Multifunktionsbauteile über eine greifbare Größe. Zur Montage genügt das präzise Ausrichten des All-In-One-Teils auf dem Gehäuse. Anschließend werden die Bauteile manuell oder – bei entsprechenden Serien – maschinell eingedrückt.
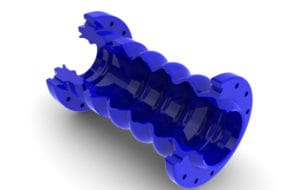
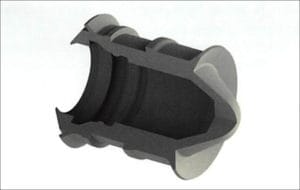
Ventilspitze von SKF Economos.
Die All-In-One-Technik kann jedoch noch mehr: Sie ermöglicht auch die Beseitigung von Toträumen zwischen Aufnahmenut und Dichtelement. Das ist wichtig bei aseptischen Dichtungsauslegungen im Food- und Pharmabereich. Mit den Werkstoffen der Ecopur-Familie lassen sich zudem straffe und mechanisch ausreichend belastbare Grundkörper (z. B. Ventilkolben) mit dünnen, flexiblen Dichtlippen realisieren.
Zusätzliche Gleit- und Führungsflächen lassen sich mit den Werkstoffen S-Ecopur, PTFE oder PE leicht erzeugen. Mit S-Ecopur steht ferner ein Werkstoff zur Verfügung, der über eine integrierte Festschmierstoffkombination verfügt. Ausgesparte Nuten zur Aufnahme von zusätzlichen Führungselementen können konstruktiv mit vorgesehen werden.
Bei der Serienfertigung von All-In-One-Dichtungen besteht die Option kundenseitiger Modifikationen wie die Anbringung zusätzlicher Fertigungshilfen oder Kennzeichnungsrillen und Markierungsflansche zur Absicherung und Erkennung. Rollwülste dienen zum sicheren Separieren beim Rollen über Sortierleisten durch Schwingförderer; hierdurch kippen die Bauteile einseitig ab.
Nicht zuletzt führt auch die vergleichsweise einfache Logistik bei All-In-One-Bauteilen zu einer vorteilhaften Kostenbetrachtung: So werden Lagerplätze und deren Pflege eingespart. Beschaffungsaufwände für Einzelprodukte, die sonst meist von unterschiedlichen Partnern bezogen werden, entfallen. Auch unter Nachhaltigkeitsgesichtspunkten ist dies ein interessanter Aspekt.
Grenzen für die Umsetzung von All-In-One-Dichtungslösungen setzen in der Praxis bislang vor allem Extremwerte bei Druck, Gleitgeschwindigkeit und Temperatur. So können hohe Seitenkräfte unter Umständen nicht durch den Grundkörper aus Dichtungswerkstoff abgefangen werden. Eine Kolben-Konstruktion aus Metall mit aufgelegten Gewebebändern ist hier die gebotene Alternative.
Vielversprechend und zukunftsweisend erscheint aber auch die Kombination mit Mehrkomponententechnik (2K/3K), mit der es möglich ist, die Werkstoffeigenschaften des Bauteils zu variieren. SKF Economos verfügt über das selbstentwickelte SKF Seal-Jet-Fertigungsverfahren für geringe Stückzahlen, mit dem in der Design- und Entwicklungsphase schnell und kostengünstig Muster- oder Kleinserien erstellt werden können.
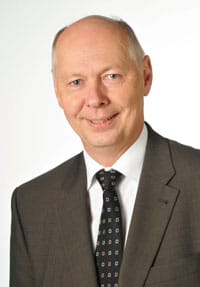
In Deutschland stellt SKF (vertreten durch die SKF Economos Deutschland GmbH, Bietigheim-Bissingen) zur schnellen Entwicklung und Realisierung von Dichtungs- und Fluidlösungen mit insgesamt 19 Niederlassungen und Verkaufsgebieten eine flächendeckende Vor-Ort-Betreuung mit kurzen Wegen sicher. Mit dem Konzept „Innovation in einem Tag“ wird die schnelle Entwicklung und Realisierung von Dichtungs- und Fluidlösungen ermöglicht.
Anfragen an den Hersteller sind jederzeit und bequem per Smartphone-App möglich unter http://goo.gl/MfiWq (Android) oder http://bit.ly/1ri1OES (iOS).